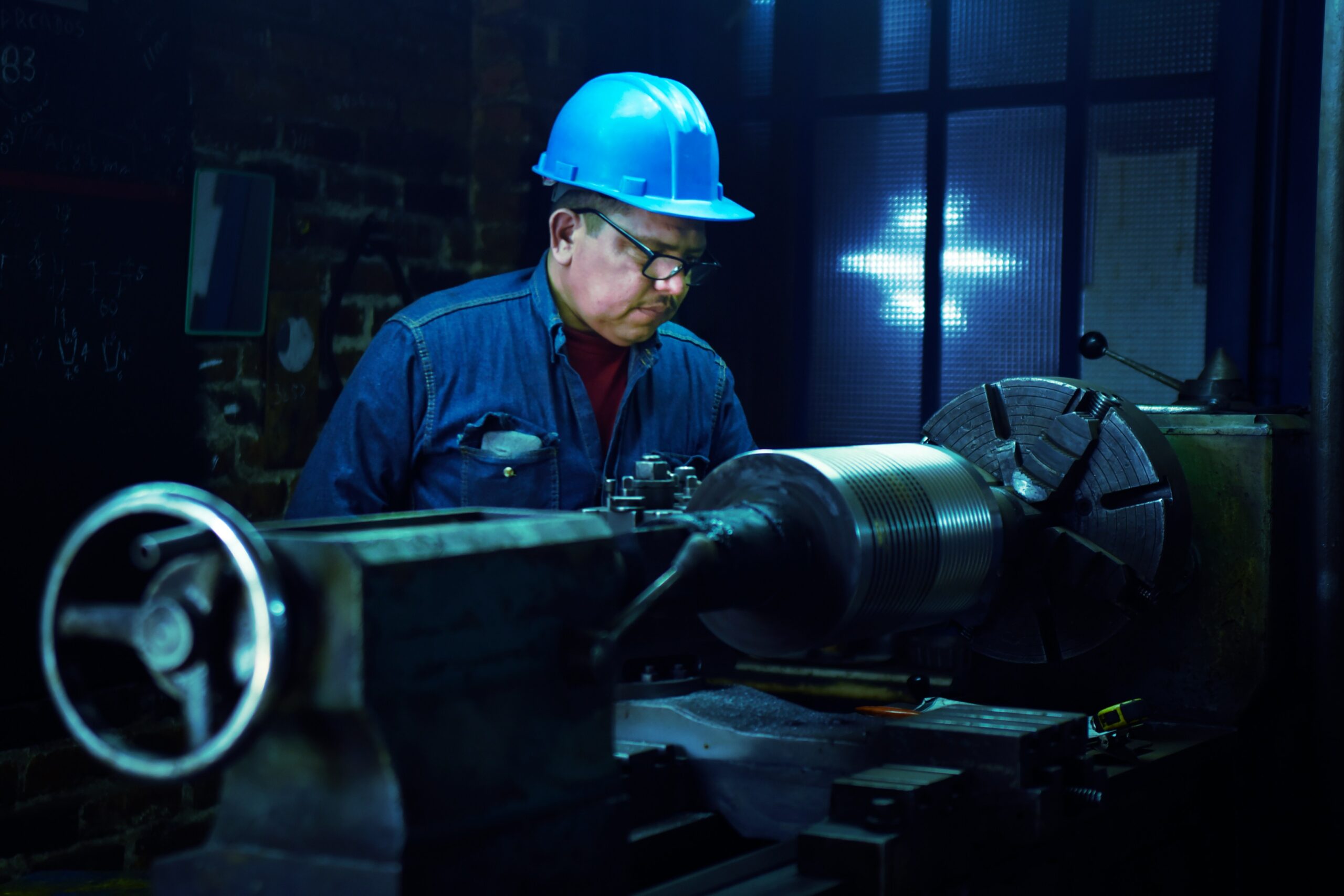
Implementing a robust Quality Management System is crucial for organisations operating across multiple sites to maintain consistency, efficiency and safety.
Key benefits of a multi-site QMS
- Establishing uniform processes and procedures, reducing variability in quality and performance across sites.
- Streamlining workflows, eliminating redundancies, establishing best practices and optimising resource allocation, all leading to improved efficiency and cost savings.
- Facilitating knowledge sharing and expertise across sites, enabling quick resolution of quality issues and replication of successes.
Single-site vs Multi-site QMS
A single-site QMS is usually designed around the requirements of a specific location without the need to consider any geographic or operational variation
In contrast, a multi-site QMS implementation tends to focus on standardising processes and controls consistently applied throughout multiple locations of an organisation, ensuring a unified quality management framework across all sites. However, there may still be different process requirements between sites, which also need to be addressed.
Recognising these differences is essential for organisations looking to optimise their quality management approach and align it with their operational structure.
The good news is that Singlepoint is equally suitable for either scenario!
Benefits of multi-site QMS implementation with Singlepoint
Implementing a multi-site QMS using Singlepoint offers organisations a comprehensive solution to streamline quality management processes. By leveraging Singlepoint’s advanced features and capabilities, Quality Managers can unlock a range of benefits beyond the inherent advantages of a multi-site QMS.
Reduced infrastructure and maintenance overheads
One of the key advantages of implementing a multi-site QMS with Singlepoint is the reduction in IT infrastructure and maintenance requirements. Singlepoint’s web-based platform, whether hosted on-premise or in the cloud, eliminates the need for extensive on-premise hardware and software, simplifying the deployment and management of the QMS across multiple sites. This reduces the initial investment and minimises ongoing maintenance costs and IT resource burden.
Easy and intuitive access
A multi-site system can only deliver its potential value with mass end-user engagement. Singlepoint’s intuitive Visual Navigator enables seamless collaboration and communication between sites, making it easy for quality teams to access and share information, documents, and best practices across multiple physical locations. This fosters a culture of knowledge sharing and continuous improvement.
Single source of truth
With Singlepoint, organisations can centralise their document and knowledge management using Singlepoint DMS, ensuring that all sites have access to the latest quality documentation, procedures and guidelines. This centralised repository eliminates the need for manual document distribution and reduces the risk of using outdated or inconsistent information. Teams can efficiently control and manage documents, making it easier to maintain compliance and audit readiness across all sites.
Multi-Language Support
Singlepoint offers multi-language support in the interface, allowing users to translate the system into multiple languages, including forms and grids. This enables users to work in their preferred language, enhancing accessibility and user adoption. Additionally, Singlepoint’s generative AI capabilities can assist with document content summaries, understanding content and even translating document content into multiple languages.
Real-time quality metrics and reports
Singlepoint’s Business Intelligence tools provide real-time visibility into quality metrics and performance across all sites. Quality managers can access dashboards and reports that offer actionable insights into key performance indicators, allowing them to identify trends, monitor progress and make data-driven decisions. Different levels of seniority can also benefit from real-time dashboards tailored to their needs, either looking at a combined picture of multiple sites or drilling down into localised views. This enhanced visibility enables proactive quality management and facilitates the identification of improvement opportunities.
Site-specific customisation
While Singlepoint enables the design and control of processes suitable for the entire organisation, it also offers the flexibility to accommodate site-specific requirements. Sites can create tailored workflows and approval processes that meet the unique needs of each location, ensuring compliance with local regulations and standards. This adaptability is crucial for organisations operating in diverse geographical regions or industries with varying quality requirements.
All-in-one updates
Singlepoint’s web based solution allows the rapid dissemination of updates and improvements to the QMS across all sites. As Singlepoint consistently releases new features and functionality, quality managers can easily incorporate these enhancements into their processes. This ensures that the QMS remains up-to-date and aligned with industry best practices, regulatory changes and evolving organisational needs.
Integration with Existing Systems
Singlepoint provides REST APIs and connectors for popular business systems such as ERPs and CRMs, enabling seamless integration with an organisation’s existing IT landscape. Moreover, Singlepoint can support custom integrations with site-specific tools and databases, ensuring that the QMS is well-integrated with unique systems and processes at each location.
Planning your multi-site QMS implementation
Here’s an overview of the key steps involved in planning a multi-site QMS implementation:
Assessing the landscape
The first step in planning your multi-site QMS implementation is to identify and prioritise your organisation’s key quality objectives and targets. Engage with senior management and stakeholders from each site to gain a deep understanding of their expectations and requirements.
Determining the Scope
With a clear understanding of your organisation’s quality objectives, the next step is to determine the scope of your multi-site QMS. This involves identifying the sites and business units that will be included in the implementation, as well as defining the boundaries and interfaces between them. Consider factors such as the size and complexity of each site, the nature of their operations and the degree of interdependence between them. Engage with site leaders and process owners to validate the scope and ensure buy-in across the organisation.
Your vendor should be able to support with this. Our team of industry experts have deployed hundreds of Singlepoint systems across many different industries and can help ensure a successful project outcome.
Evaluate against requirements
To develop an effective multi-site QMS, it is crucial to evaluate the organisation’s current processes and systems against the requirements of the chosen quality standard (e.g., ISO 9001) and industry best practices. Conducting a thorough gap analysis helps identify areas where standardisation and harmonisation can be achieved across sites. This assessment involves evaluating the maturity and effectiveness of existing quality processes, such as document control and corrective and preventive actions (CAPA). Utilising tools like process mapping, value stream analysis and benchmarking provides valuable insights into opportunities for improvement and helps define the future state you want to achieve.
Defining roles and responsibilities
A successful multi-site QMS implementation requires the active participation and commitment of individuals from all levels of the organisation. Establish a cross-functional project team with representatives from each site, including quality managers, engineers and subject matter experts. Clearly define the roles and responsibilities of each team member, ensuring that they understand their contributions to the planning, implementation and maintenance of the QMS. Consider appointing site-specific quality champions to drive local adoption and engagement.
Allocating Resources
Implementing a multi-site QMS requires a significant investment in resources, including people and technology. Carefully assessing the resource requirements for the project and securing the necessary budget and support from senior management is crucial. This involves considering the training and development needs of team members in areas such as quality management principles, auditing techniques and the use of QMS software tools, as well as evaluating the infrastructure and technology investments necessary to support the deployment and maintenance of the QMS across all sites.
Deploying your multi-site QMS with Singlepoint
With a clear understanding of the planning steps, let’s look at how Singlepoint can support the deployment of a multi-site QMS.
Centralised Administration and Management
Implementing a single instance of Singlepoint for multiple sites provides a centralised configuration and user management console. This approach reduces IT complexity and maintenance costs by eliminating the need for site-specific installations or upgrades. Centralised backup and disaster recovery processes ensure the integrity and availability of the QMS across all sites.
Data Segregation and Security
Singlepoint supports multi-tenant or tenanted environments, enabling the logical separation of data and configurations for each site. This ensures data privacy and security, as each site’s information is protected and accessible only to authorised users.
Site-Specific Configurations and Customisation
Singlepoint allows for site-specific configurations and customisations to meet the unique needs of each location while maintaining a centralised QMS. Quality managers can define site-specific workflows, approval processes and user roles and responsibilities. The user interface and documentation can be localised to support different languages and terminology used at each site.
Global Data Sharing and Collaboration
Singlepoint enables the sharing of data pools globally, promoting collaboration and knowledge sharing across sites. Centralised repositories for documents and records ensure a single source of truth for quality documentation, eliminating duplication and inconsistencies. Real-time data synchronisation across sites allows for instant access to the latest information, facilitating informed decision-making and problem-solving. Unified reporting and analytics capabilities provide a holistic view of quality performance across all sites, enabling organisations to identify trends, best practices and areas for improvement.
Simplified User Access and Multi-Site Roles
Singlepoint supports multi-site user roles, allowing individuals to access and contribute to the QMS from multiple locations through a single interface. This simplifies the user experience and reduces login fatigue. Centralised user management and provisioning streamline the process of granting and revoking access rights based on roles and responsibilities.
Single Sign-On (SSO) Integration
Singlepoint can integrate with existing authentication systems and support multiple identity providers through SSO capabilities. This allows organisations to leverage their existing authentication infrastructure, such as Active Directory or other SSO platforms, to manage user access to the QMS. Singlepoint is compatible with standard authentication protocols, such as SAML and OAuth, ensuring seamless integration with various identity management solutions.
Multi-site implementation with Hitachi Rail
Hitachi Rail Europe, Ltd., a subsidiary of Hitachi, Ltd., is a total railway system supplier offering rolling stock, traction equipment, signalling, traffic management systems and maintenance centres. In 2015, the company selected Singlepoint to manage a variety of document control, quality and health and safety processes across their multiple sites.
Transforming Document Control at their London HQ
Paul Askew, based at the company’s London headquarters, was involved in the initial selection process for a new electronic document management system. Singlepoint’s demonstrations convinced Paul that the system could achieve his business goals, splitting out different types of documentation and making core business documentation easily accessible to all HRE staff, regardless of their location.
According to Paul, “Singlepoint has been a huge success and has delivered precisely what we wanted from the system. The adoption of Singlepoint has exceeded our original expectations.”
Implementing Singlepoint at Newton Aycliffe Facility
Andrew Brown, Quality Systems Engineer at Hitachi Rail’s state-of-the-art manufacturing facility in Newton Aycliffe, has been a key team member in implementing Singlepoint. Initially purchased for document control, Singlepoint has been deployed for much more, including engineering change, audits and the process for capturing near misses and other health and safety incidents.
Andrew praised the ease of designing workflows and forms in Singlepoint, stating, “Designing your own workflows and forms in Singlepoint is really easy in my opinion and is very logical to follow and easy to tailor. This is great because it allows us the flexibility to modify the existing modules and also means we are free to crack on with designing our own solutions whenever we want to.”
Incident Management at Ashford Train Maintenance Centre
Peter Burge, SHEQ Manager at Hitachi Rail Europe’s Ashford Train Maintenance Centre, was responsible for implementing Singlepoint for document control and Incident Management. The previous manual system was inefficient and provided no control over processes or access to meaningful data.
With Singlepoint, Peter noted, “It’s very easy to use, very intuitive and quick to get information in and out of the system.” The graphical setup allows users to find documents quickly and the automated incident reporting process has completely transformed their approach. Real-time information and tracking of task completion have been significant wins for the organisation.
Looking Forward
Across different locations and responsibilities, the feedback for Singlepoint has been consistently positive. Its user-friendly interface, easy accessibility and effectiveness have made it an integral part of operations at Hitachi Rail Europe. As the journey continues, there is exciting potential for Singlepoint to transform even more processes across the organisation.
Throughout this guide, we have explored the key benefits of implementing a multi-site QMS and how Singlepoint can support your organisation in achieving operational excellence and continuous improvement across all locations.
By leveraging Singlepoint’s advanced features and capabilities, you can streamline quality management processes, reduce infrastructure and maintenance overheads, facilitate collaboration and knowledge sharing, and ensure site-specific customisation while maintaining a centralised QMS.