Advanced Product Quality Planning.
Advanced Product Quality Planning (APQP), when done properly, can yield huge benefits in terms of product and process quality and on-time product launch.
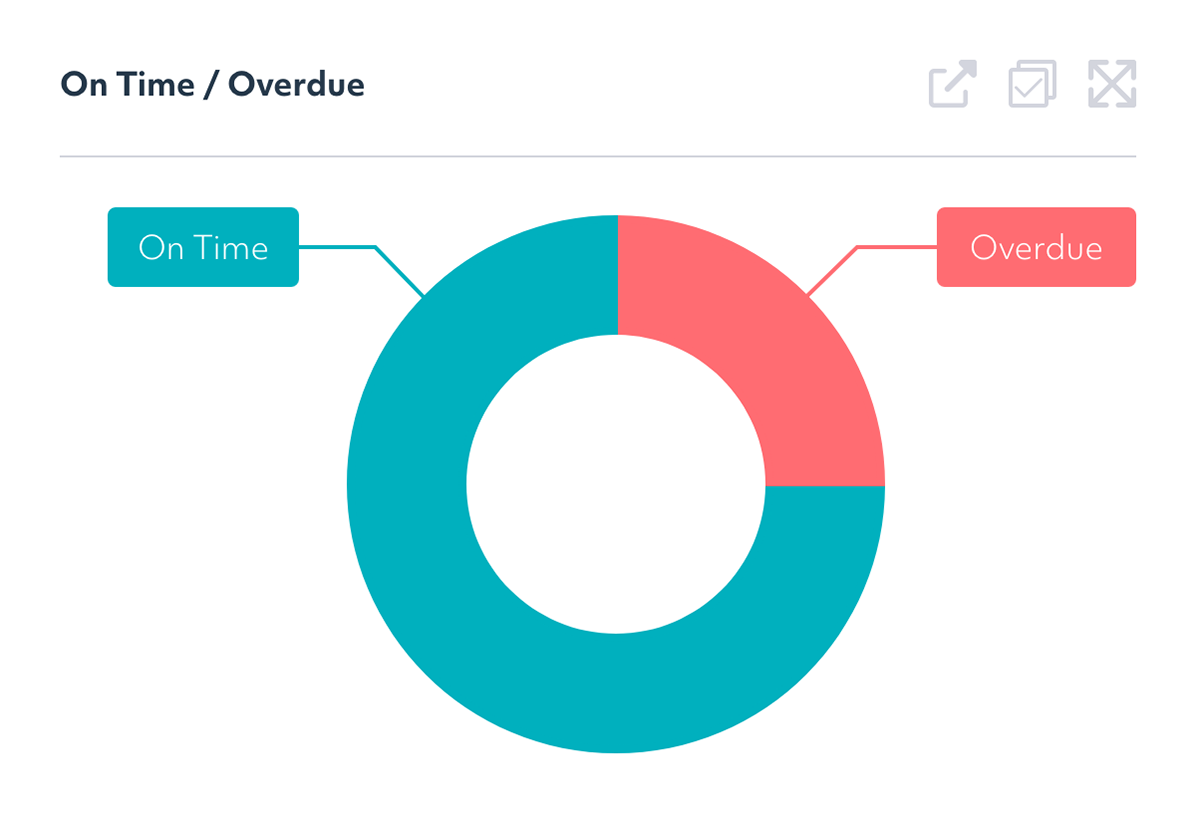
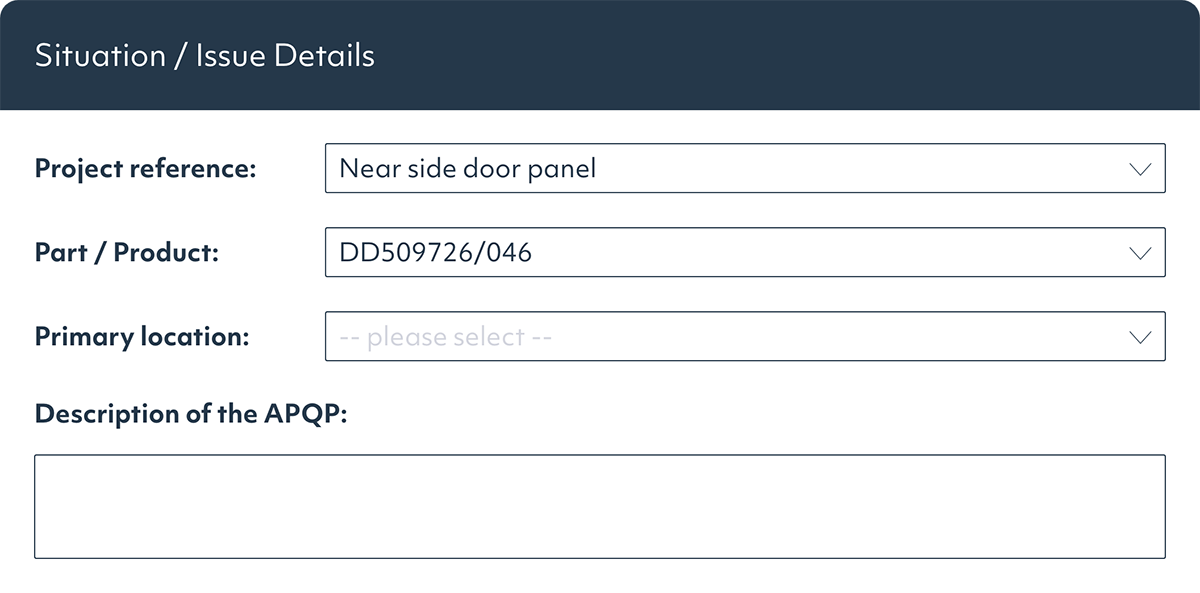
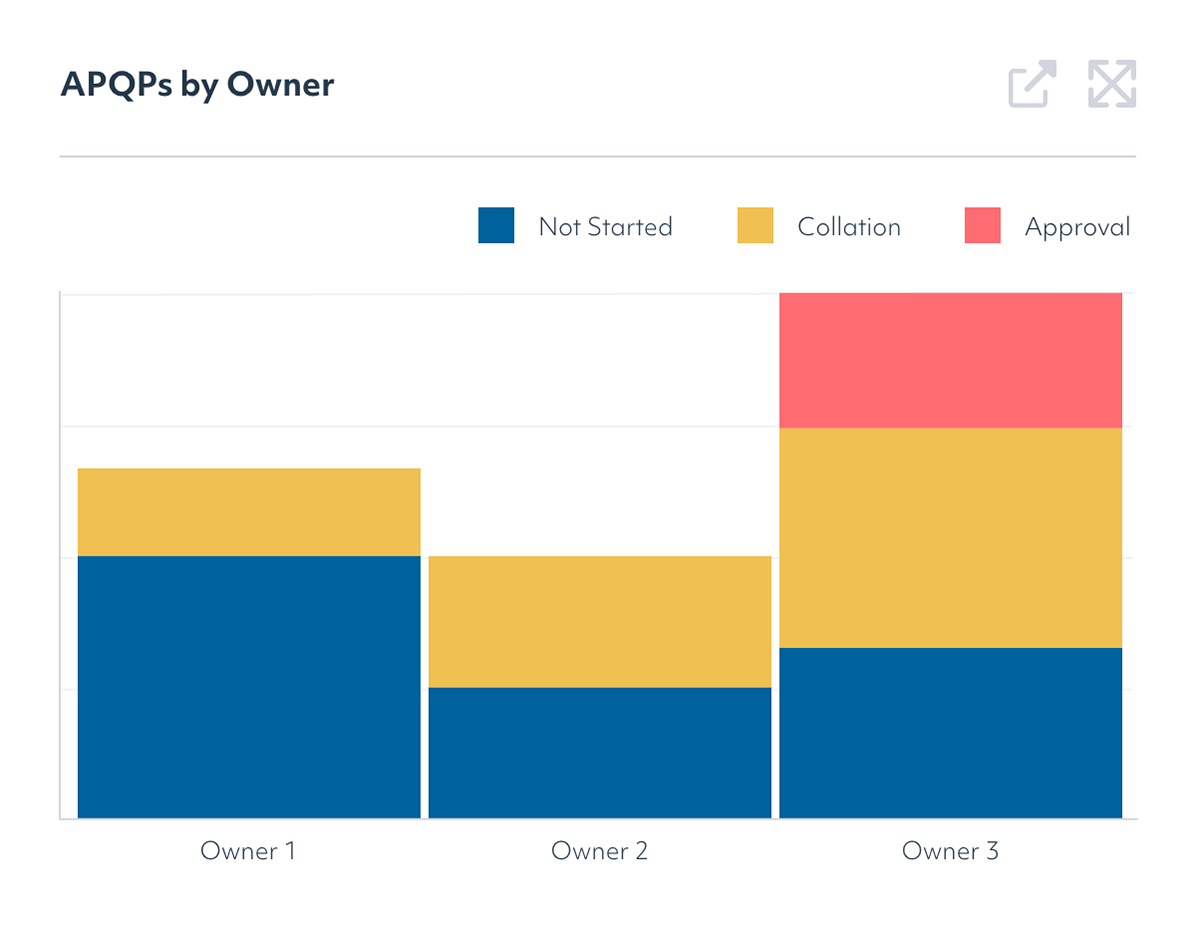
Top-level benefits
The challenge is that APQP is often a mandated process from your customer and it can soon become a burden to your organisation if you manage and execute the process manually. Singlepoint’s APQP module gives you the opportunity to be on top of this process and to truly extract the full range of benefits it has to offer.
Ensure accurate & consistent data
Singlepoint APQP manages all data in SQL. This allows organisations to re-use the data as and where needed with the certain knowledge that the data is correct across all of your documents and references.
Cross-functional yet secure team collaboration
Organisations have the ability to manage permissions and user access, allowing multiple users to view information in a secure, but still collaborative, manner.
Save time vs. manual spreadsheets
The ability to re-use work and data is front and centre in our APQP module; for example, we have a Process Library, pre-populated with the various references required across Control Plan and Process FMEA, ready for you to select and watch as Singlepoint builds your documents and your project.
Data-driven documents
Singlepoint runs on smart, data-driven documents that know their own content and inter-relate to other suite documents, covering:
Process library
Our APQP module includes a process library with all references required for control plan, PFMEA and characteristics list. Simply select the processes you need and sit back and let Singlepoint build the documents and the project pack for you. Easily import existing data from excel.
Centralised data management
Data is managed centrally throughout Singlepoint. This means that if you change a reference in, for example, the characteristics list, the change will be propagated throughout the project automatically. This includes a full approval process and full audit trail, which is fully integrated with Singlepoint’s Document Management System.
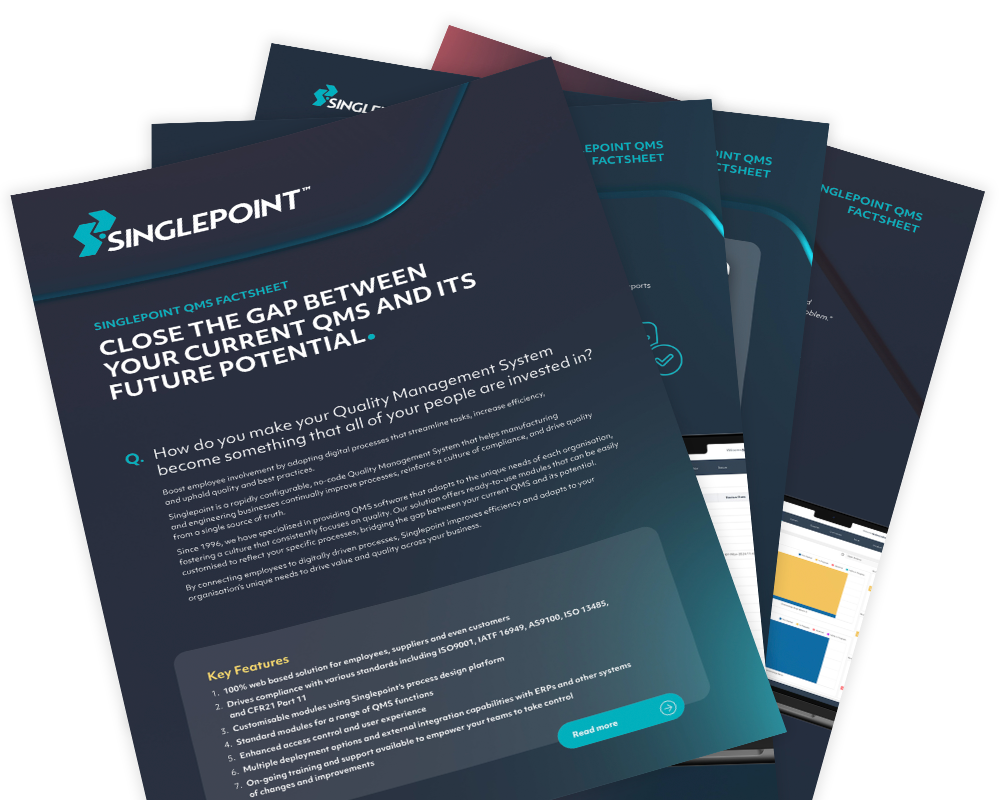
Get our QMS factsheet
Download our factsheet to learn more about how Singlepoint’s quality management software can help you.
Case studies
FAQs
What is APQP in manufacturing?
APQP stands for Advanced Product Quality Planning. It is a product development process, often employed between customer and supplier, with the goal of producing a quality plan that will support the development of a product or service. Heavy emphasis is placed on evaluating and eliminating substantial risk from the process and product design and in gathering supporting documentation as evidence of such activities.
What are the 5 phases of APQP?
- Phase 1: Plan and Define
- Phase 2: Product Design and Development
- Phase 3: Process Design and Development
- Phase 4: Product and Process Validation
- Phase 5: Feedback and Continuous Improvement
Why should you invest in APQP software?
APQP software allows you to access a transparent, complete and real-time view of your APQP processes across your organisation. Through understanding issues immediately and proactively managing them, you can avoid delays in production and reduce abnormalities/failures, leading to increased production velocity and decreased wastage costs.