About the client
Acdopro have been using Singlepoint since May 2020. They specialise in the manufacture of laundry products exported to over 75 countries, under well-known trademarks such as Dr. Beckmann, Glo white, Stain Devils and ACDO.
Acdopro use Singlepoint for multiple modules including document control, issue, calibration, visual navigator, and a Scale Data Collection custom module. We caught up with Acdopro’s Technical Manager, Jack Hough, to find out a little more.
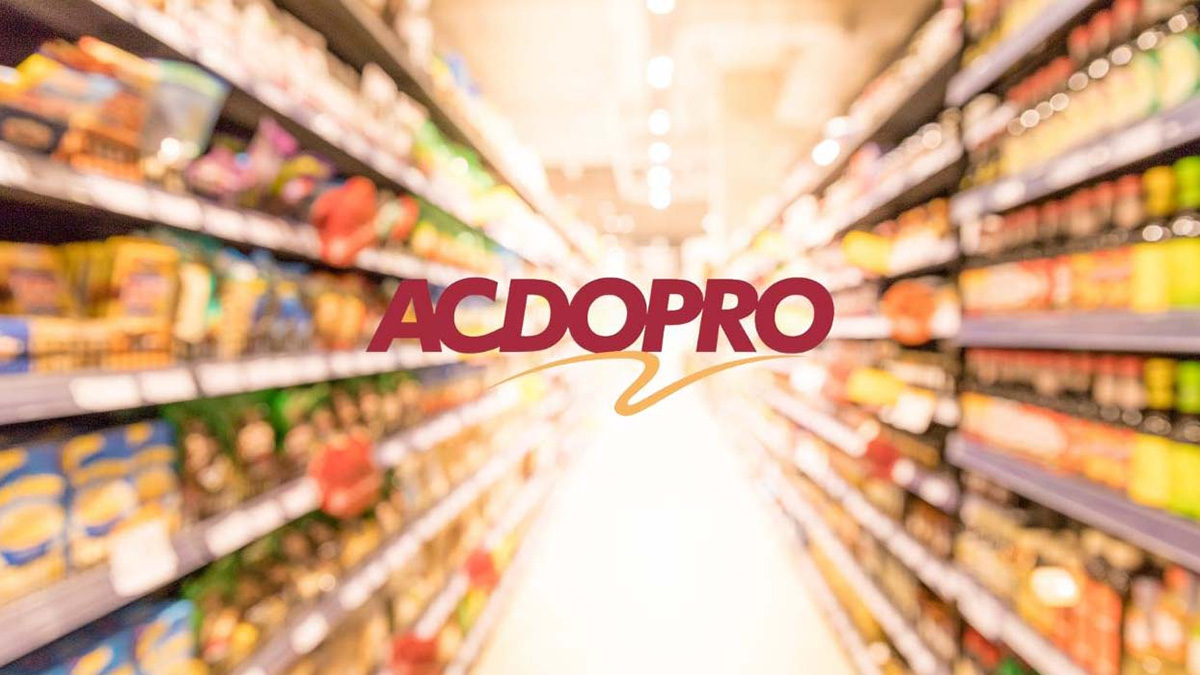
So, Jack, you are using Singlepoint for a lot of modules. Do you have them all implemented already?
No, I wanted to roll out the modules one by one, so I’m getting ready to implement audit, training, competency, and incident management. We’ve had quite a turnover of staff in the past year due to one thing or the other and people who I’d trained have now left. Once I’ve trained the new members of staff in the different elements, they will be brought online.
You’ve used Visual Navigator to create bespoke dashboards for the staff. What sort of elements have you incorporated?
The majority of people use the same dashboard, but I’ve also created bespoke ones for managers. Our design team created the look of the dashboards and through Visual Navigator, I was then able to create the ‘hotspots’ which connect to documents at the click of a button. We have buttons which go to filter folders, another goes to a ‘site’ map and the user can then click on a particular department and be taken to filter folders of relevant documents. There’s also a button which takes the user to the Scale Data Collection module (most of our users use that module) and there’s also a button to get to the reports for that. For the managers, I’ve created a slightly different dashboard which also shows that there are documents requiring action, with the number of documents waiting.
What do you see as the benefits of having a custom module created for you (the Scale Data Collection module)?
We were using a piece of software which ONLY did the Scale Data Collection. With Singlepoint, we have a whole package which incorporates many modules, but we were also able to remove elements of our old system which weren’t needed and add new requirements. The users feel that it’s miles better. They can now see if they’ve made a mistake and can rectify it. Alarms can now be raised for a production line, and everybody can see where the issue is from the software, rather than having to go onto the shopfloor to locate the alarm. Some quality ‘near misses’ have been automated and they go directly to the Issue module. It’s speeded up the previous process and added extra functionality, so it’s become more efficient. Our reports are created every 30 minutes on every production line (we have 6 running at once).
“It’s very easy to use, very intuitive and quick to get information in and out of the system”
You’ve also been using document control. How has that been improved by using an electronic process?
We previously had a process of signing in new products on a sheet in a folder with various physical signatures required. This needed to go around multiple departments and could quite easily get lost, so people were ‘skipping’ procedures if they didn’t want to wait. Now we’re able to use a simple sign-off with automated emails so the managers know that documents are awaiting approvals. As the manager’s dashboard that has been created also shows these documents, it’s a ‘belt and braces’ approach.
Are there any other modules that you’d like to change from a manual process?
Yes, I’d like to create a LIMS system for laboratory information. It’s only simple chemical testing and with some training from Syncronology, I should be able to create that. Syncronology are aware that I want this training and are happy to talk to me about this when I’m ready.
How satisfied are you with the service you receive from Syncronology?
It’s been good so far. With training starting at the beginning of the Covid-19 pandemic, the sessions have all been done remotely which has benefitted us as we had sites in Germany that wanted to take part. Being able to record the sessions has been invaluable as I wanted to be the first port of call for users and if I’ve been unsure, I’ve been able to look back at the videos. Another upside is that I’ll be able to edit the videos into sections and then make them available to the users.
Why did you choose Singlepoint over other software you’d seen?
I didn’t see that many products as I wanted something specific. I’d been using another product that Syncronology support in my previous company so I wanted to see what Singlepoint could do. I didn’t find another package that could give me as much as I wanted, but which also showed me modules that I didn’t know I needed but did! Also being able to see how a customised module could work on the demonstration was a big win.
Please describe some of the benefits of Singlepoint to you.
We’ve been able to integrate a lot more things and automate processes like ‘actions’ in issues, which didn’t get followed up previously. Singlepoint gives easy visualisation of what stage a process is at and who is responsible. There’s also great visibility. Users were previously able to ‘hide’ issues or outstanding tasks but it’s now completely transparent. Managers can now see what’s outstanding and it can be escalated, mainly on the Corrective and Preventive Action (Issue) module. We’ve never been able to do that in the past and it’s really improved efficiency. We are due a 3-year audit shortly and in the previous audit I was able to show them what I was aiming to achieve. They loved the idea and said that the integration of Singlepoint would be beneficial.
We asked Jack for a final comment.
“I’m really happy with it – I’d come and help you develop it further if that was an option”!