About the client
Fablink, a key player in the automotive, commercial, and heavy plant vehicle sector, has been utilising Singlepoint for New Product Introduction (NPI) and Advanced Product Quality Planning (APQP) since August 2011.
Catering to a specialised team of 25 users, Fablink has effectively harnessed the capabilities of Singlepoint to enhance its product development processes.
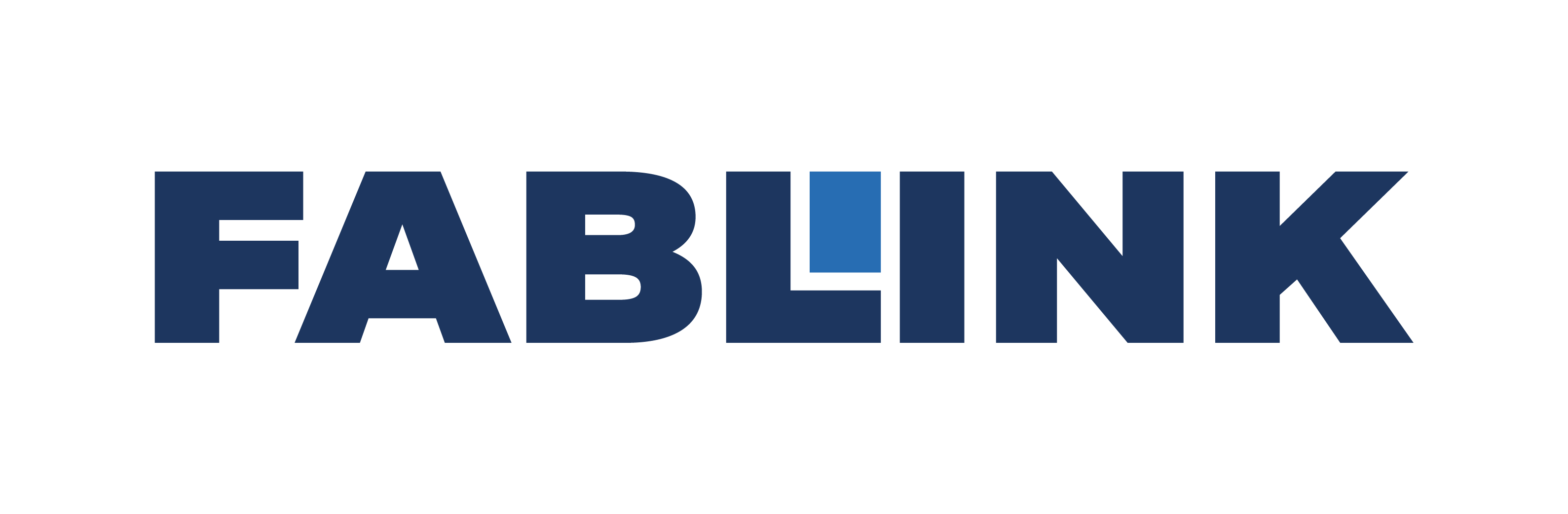
The challenge
Before Singlepoint, Fablink’s approach to managing its NPI and APQP processes was fragmented and inefficient.
With a mix of MS Project for some and Excel for others, the team struggled to stay synchronised, leading to a lack of visibility and manageability over tasks and progress.
Our solution
The implementation of ProjectPoint, part of Singlepoint’s suite, revolutionised Fablink’s project management. They now have the flexibility to import MS Project files into Singlepoint or start new projects independently, utilising templates within ProjectPoint. This has provided the team with a real-time collaborative environment and full process visibility.
The Results
With Singlepoint, Fablink has transformed its NPI and APQP processes, offering a clear view of tasks, issues and risks, ensuring they are addressed promptly.
“We have 100% visibility into everyone’s tasks and issues and we can manage any risk in plenty of time to keep things on track,”
John Butler, Head of Quality & Engineering at Fablink.
The system has been instrumental in enabling Fablink to consistently deliver exceptional products to their customers on time.