About the client
Hitachi Rail Europe, Ltd. is a wholly owned subsidiary of Hitachi, Ltd. and a total railway system supplier offering rolling stock, traction equipment, signalling, traffic management systems and maintenance centres.
In 2015, the company selected Singlepoint to manage a variety of document control, quality and health and safety processes. Three years on, we are delighted to report that Singlepoint has delivered on every front and here we are able to provide some of the back story and the detail around this impressive project.
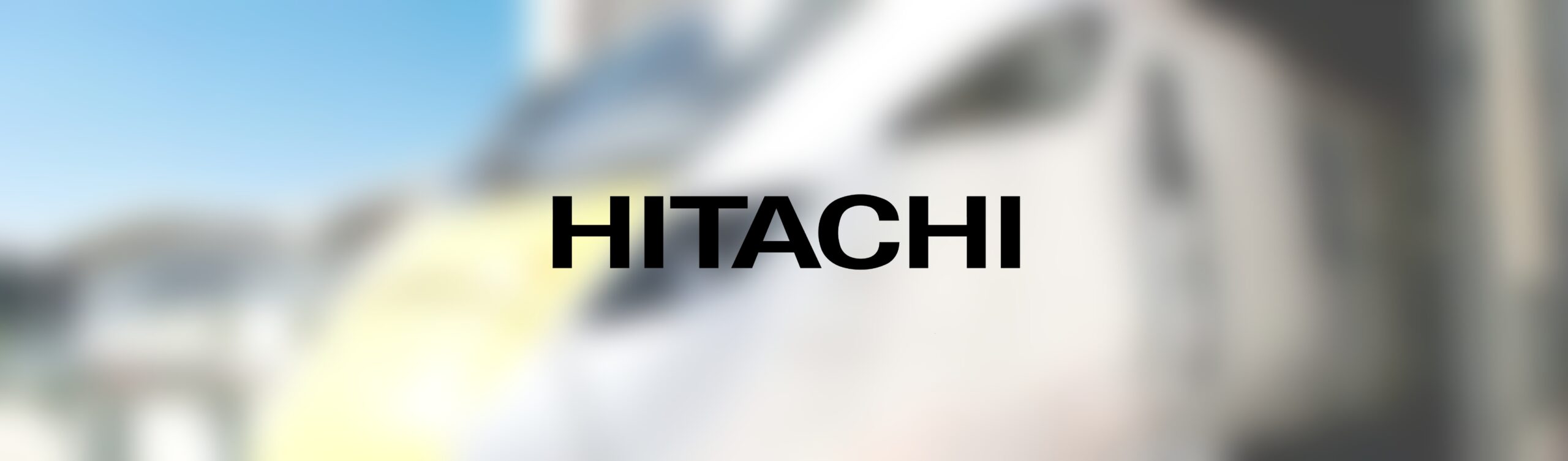
Transforming Document Control
Paul is based at the company’s London headquarters and was involved in the initial selection process for a new electronic document management system back in February 2016. Clearly, our demonstrations of Singlepoint helped persuade Paul that this was a system he could rely on to achieve his business goals and when we recently caught up with him we were delighted to hear that that faith has proved to be very well placed.
We asked Paul to remind us of the original goals for the product and what the business problems were that he wanted to solve; “At the time, we had a very old centralised document management system that contained different types of documentation such as engineering documents, project as well as core business documents. Not only that, the licensing was such that it was not possible for users to access the documentation they needed to get at. So, we had two basic goals: firstly, we needed a way of splitting out these documents and making the core business documentation independent from the others and secondly, a system that would be easily accessible and available to all HRE staff, wherever they were in the country and further afield.
“Singlepoint has been a huge success and has delivered precisely what we wanted from the system. In fact, the adoption of Singlepoint has exceeded our original expectations”
“To that end, Singlepoint has been a huge success and has delivered precisely what we wanted from the system. In fact, the adoption of Singlepoint has exceeded our original expectations. For example, as the company grew and we added more Train Maintenance Centres (TMC’s), we identified the need to not only provide the entire business with Levels 1 to 4 documentation, but each TMC with its own Level 5 document library, which means that we have safety critical and maintenance documentation all under control as well.”
“One of the main attractions to the Singlepoint system was the Visual Navigator front-end and this has been massive for us.”
Paul’s role as Senior Document Controller sees him at the front line of surveillance and customer audits, so we were interested to hear how Singlepoint had been received by the auditors; Paul added “We have had several audits since Singlepoint has been implemented, usually lasting for two or three days with one entire day spent auditing our document control system and I can tell you that Singlepoint has stood up extremely well. The feedback from the auditors has been very, very positive. Singlepoint manages the entire document life- cycle and so we can easily show that we are on top of things such as formal review processes. The suite of management reports within the system gives us immediate access to usage information which in turn helps us pinpoint which documents are being used and, probably more importantly, which ones are not.”
At Syncronology, we know how daunting it can be to implement a new system on such a large scale and we put a lot of emphasis on supporting our customer through the entire process, not just during the initial phases but on an ongoing basis and Paul was happy to endorse this; “The support we have received from Syncronology has been outstanding. Yes, the system is intuitive and easy to use but as with all things there are always challenges and questions and my queries to the technical support team at Syncronology have always been responded to quickly and positively and we have jointly devised many innovative ways to further improve on the use and usefulness of the system. They have been a real pleasure to work with.”
Paul rounded off our brief catch up by adding “In summary, Singlepoint has been a huge leap forward for us. The tool is incredibly flexible and adaptable and has moved the business on immeasurably from where we were a couple of years ago. We have achieved more with the document control module than we thought and it has also been great to deploy other modules within the suite such as the Audit Manager module, Incident Manager module and also the Engineering Change Manager module.”
Singlepoint at the client’s Newton Aycliffe Facility
When Hitachi Rail (Europe) built their huge new state-of- the-art manufacturing facility in Newton Aycliffe, County Durham, we were delighted to be invited in to showcase Singlepoint’s capabilities for document control, and even more pleased to be awarded the contract back in 2015.
“Singlepoint does what we need it to do and the support is brilliant!”. We couldn’t have put it better ourselves”
Since then, Singlepoint has been implemented not just for document control but for various other quality management and health and safety management processes. Andrew Brown, Quality Systems Engineer at the Newton Aycliffe facility, has been a key team member for implementing Singlepoint. We recently caught up with Andrew and asked him about his experiences of using Singlepoint, starting off with his recollections of the early months of working with the software. “When we first purchased Singlepoint, the intent was to use the system very much for document control, but in fact we have deployed it for much more besides.
“Singlepoint does what we need it to do and the support is brilliant!”. We couldn’t have put it better ourselves”
“When I first saw Singlepoint, it was clear that the software was capable of being utilised for multiple activities which gave us many ideas for development and from those early ideas, Singlepoint has grown into a system that handles not just document control but also engineering change, audits and our process for capturing near misses and other health and safety incidents. The speed with which it grew was quite staggering.”
At the heart of Singlepoint is a very powerful business process design platform which features workflow, forms and reports tools and Andrew, with minimal training, took to designing his own Singlepoint modules very quickly indeed. “Designing your own workflows and forms in Singlepoint is really easy in my opinion, and is very logical to follow and easy to tailor. This is great because it allows us the flexibility to modify the existing modules and also means we are free to crack on with designing our own solutions whenever we want to.”
The deployment and technical teams at Singlepoint also came in for high praise from Andrew adding that the levels of support have been excellent. Naturally, we are absolutely delighted with the project so far at the Newton Aycliffe plant, and we look forward to a long-lasting partnership with the team.
As Andrew perfectly summed up “Singlepoint does what we need it to do and the support is brilliant!”. We couldn’t have put it better ourselves!
Implementing Singlepoint at Ashford Train Maintenance Centre
Peter Burge, SHEQ Manager for Hitachi Rail Europe at their Ashford Train Maintenance Centre, was responsible for the implementation of Singlepoint at the Ashford location covering document control and Incident Management.
Previously, incidents ranging from near misses, accidents, environmental issues et cetera were reported using completely manual systems which were ultimately recorded on a spreadsheet. According to Peter, this approach was not at all efficient and in no way gave them either the control over the processes or any access to meaningful data.
“It’s very easy to use, very intuitive and quick to get information in and out of the system”
When Singlepoint was introduced Peter could immediately see the potential of an automated system and was delighted with the subsequent results. “Singlepoint has been a really good success. It is very widely used by the users here, approximately 100 on-site, and I think that’s because it’s very easy to use, very intuitive and quick to get information in and out of the system”, Peter says.
“We use Singlepoint for accessing a wide variety of control documents and we can find what we want within one or two clicks, which is brilliant. We will be putting many many more documents into Singlepoint in the coming months and years. Users really like the graphical way it’s been set up because it means they can find what they want really quickly and easily, and I think that is critical”.
The system went live in May 2016 and since then users have been adopting Singlepoint for both accessing control documents but also for reporting health and safety related incidents and issues. Our implementation team worked very closely with Peter to design workflows, forms and reports that completely reflected the way Hitachi Rail Europe wanted the process to work.
Peter takes up the story; “Compared to the old way we used to report issues, which was literally fire a paper docket”
Singlepoint has completely transformed the way we approach this. Users have a simple report button on the intranet site which takes them directly to a series of very simple forms and that immediately kicks off a real-time workflow complete with notifications and so on.”
“From then on it’s a case of really letting the system do it for you as the correct flows are predesigned into it. This also means that we can access real-time information and we are finding that more and more people, especially in management positions, are able to dip in and out of the system to retrieve data accurately and quickly and for us that has been a big win.”
“The workflows also ensure that we can track the completion of tasks and we can monitor the whole process from start to finish and even have the system automatically escalate issues as and when needed. I would also give praise to the support we have received from Syncronology; their implementation team have been brilliant and have done a fantastic job in helping us set up the system and get it off the ground.”
When asked what he felt was the best thing about Singlepoint Peter pointed out the importance of ease-of-use for end-users; “Overall, I think the accessibility of Singlepoint is the key thing. The users like using it; it looks good, it’s intuitive to use and people can get the job done quickly.”
Looking Forward
Across different locations and responsibilities, the feedback for Singlepoint has been consistently positive. Its user-friendly interface, easy accessibility, and effectiveness have made it an integral part of operations at Hitachi Rail Europe.
The software has successfully navigated audits, received acclaim from management and has been instrumental in transforming business operations.
As we continue our journey with Hitachi Rail Europe, we’re excited about the potential for Singlepoint to transform even more processes across the organisation.