About the client
Metrol Technology Ltd, based in Aberdeen, is a key player in the oil industry, providing data monitoring and flow control solutions for production wells. The company has been utilising Singlepoint since 2014 and has onboarded over 150 users.
Having implemented it for issue management, audit management, document control and numerous custom modules created in-house, Calibration Manager has also become a key driver of efficiency and success for the company
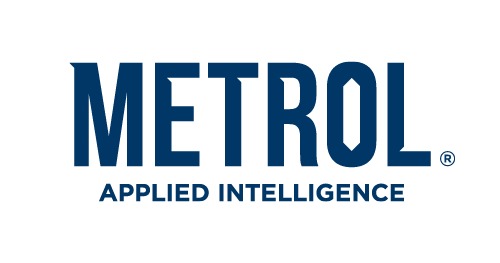
The challenge
Prior to the introduction of Singlepoint’s Calibration Manager, Metrol Technology was grappling with challenges arising from the manual handling of calibration data across several departments.
They depended on multiple spreadsheets to manage a vast inventory of 700-800 gauges, callipers and other tools, which often led to coordination mishaps, overlooked calibration due dates and restricted data input capabilities.
Our solution
To counter these bottlenecks, Metrol Technology integrated Singlepoint Calibration Manager into their Singlepoint system. The solution is designed with robust features like compliance-strength control, automatic reminders for due calibration, a comprehensive historical audit trail and easy-to-use ‘quick filters’.
These configurable filters allow the user to quickly find and locate different categories of gauges or tooling etc. (e.g. gauges due for calibration) and full workflow capability against each item, e.g. calibrate in-house, calibrate externally, check out for work etc. Also, each item has its own unique full life-cycle record and there are reports which can be run from within the module.
“Previously, there were multiple departments using separate spreadsheets so it wasn’t coordinated and it was easy to miss a due date when there were 700-800 gauges, calipers etc. Singlepoint can hold much more information in its database than the simple due date and serial number that were previously stored in a spreadsheet”
Nigel Cordiner, QA Supervisor at Metrol Technology
The Results
With the introduction of Singlepoint to their operations, significant efficiency and user-friendly enhancements have been realised.
By eliminating the need for multiple separate systems, they have streamlined their process, particularly with the intuitive drop-down feature for department filtering.
The flexibility of Singlepoint is evident too. Reports inside the Calibration module can be run (one-off and automatic), but Absolute Reporting is also utilised for various other reports, which can be set up by the users themselves.
This adaptability has not only saved time but also empowered users, fostering a sense of ownership and ease in their tasks. Furthermore, Metrol’s proactive use and customization of the platform, such as the creation of unique modules post-training by Singlepoint, underscore the system’s versatility.
Metrol is also in the process of taking other manual systems such as workshop requests and tool failure reporting and working on bringing them into Singlepoint in the next 12 months.
“It is an excellent system from my point of view… We’re using Issue Manager on a daily basis, but we’ve also created our own modules. We’ve created Stop Cards, Engineering Requests, Concessions and Management of Change. We are in the process of taking other manual systems such as workshop requests and tool failure reporting and working on bringing them into Singlepoint”
Nigel Cordiner, QA Supervisor at Metrol Technology