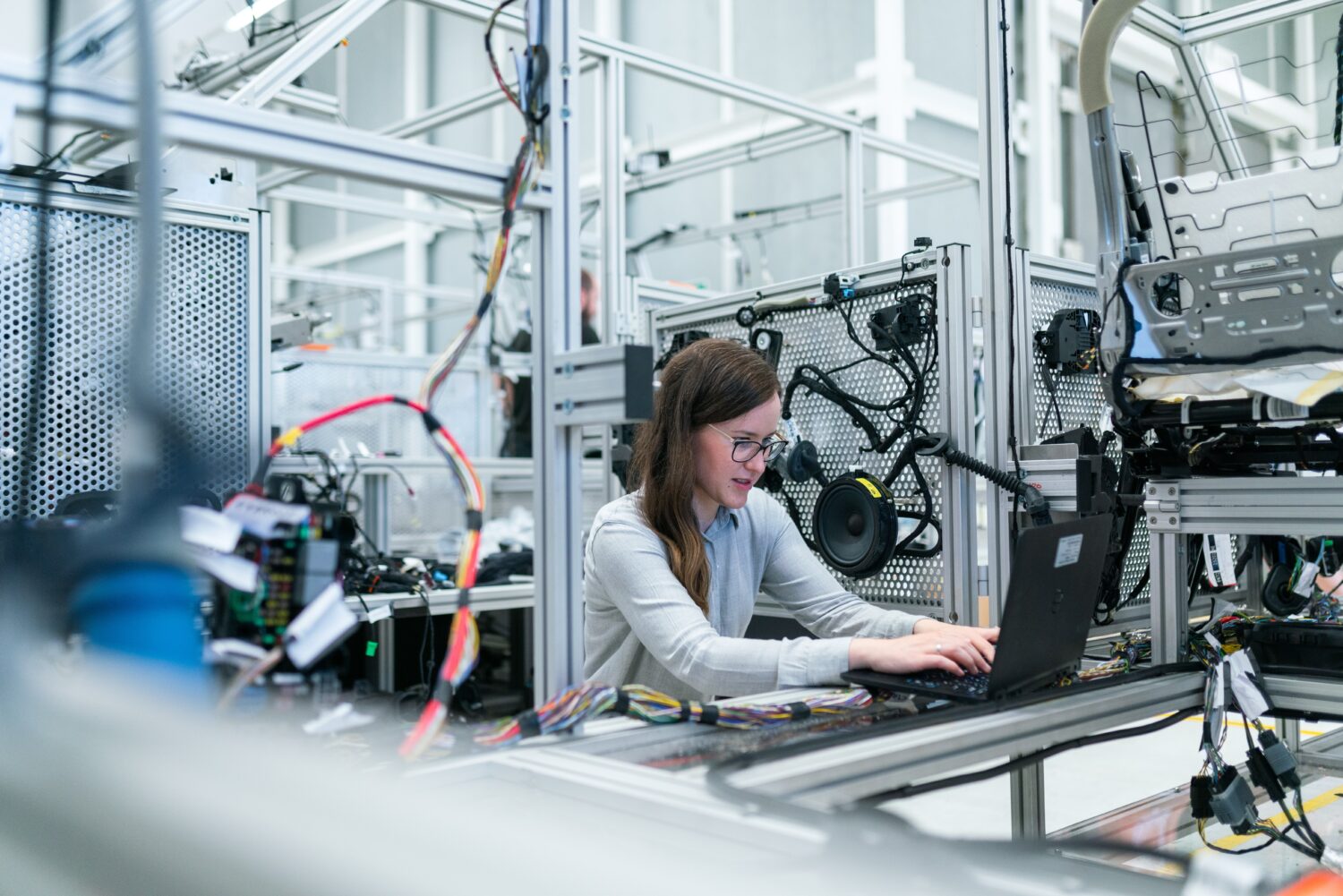
Andrew has worked in the compliance management software industry since 2000 and has worked with hundreds of companies and compliance professionals in multiple sectors across Quality, Health & Safety and Environmental management and the views and content below is drawn from those encounters from across more than two decades.
Co-founding Syncronology (now Singlepoint) in 2005 in response to a demand for adaptable, visually-oriented compliance software, Andrew has been a driving force behind Singlepoint’s development, focusing on aligning the product with market needs and ensuring it delivers tangible value to customers.
My general QMS implementation tips
From my experience, when implementing a Quality Management System it’s essential to ensure that it aligns with and enhances your business objectives. Often, QMS implementations overly concentrate on compliance. While vital, this should not be the sole focus. A more holistic approach involves integrating compliance seamlessly into your system, while prioritising efficiency, performance, and value.
The guiding principle here is straightforward: if it doesn’t add value to your business, reconsider its place in your QMS.
Also central to the success of your QMS is the role of your workforce. They are not just users of the system; they are its lifeblood. Their positive and active engagement is critical. It’s essential to avoid a scenario where the Quality department is perceived as the ‘company policeman’, a role that can foster negativity and resistance.
Instead, companies should aim for a culture where quality is a shared responsibility and an integral part of everyone’s daily activities, not an additional burden or an afterthought.
This brings us to another crucial aspect: workload management. It’s extremely important to implement a system that doesn’t overburden your employees. The goal is to embed quality and best practices into the very fabric of your operations, making it a natural part of daily tasks.
This approach helps in cultivating a mindset where quality is inherent in every action taken, rather than being seen as an extra set of annoying tasks.
Finally, communication and recognition play a significant role in reinforcing the value of your QMS. Regularly update your workforce on the system’s outcomes. Utilise smart reports and intuitive dashboards that not only provide insights but also encourage your team to continuously seek improvements.
These tools can instil a sense of ownership and pride in the quality performance of your business. Wherever possible, publicly acknowledge and praise the contributions of your workforce. This recognition not only boosts morale but also reinforces the importance of quality in every aspect of your organisation.
Why is a QMS Important?
Achieving organisational goals
A Quality Management System, at its core, is a structured approach designed to standardise procedures, processes and responsibilities, ensuring quality objectives are met efficiently.
A QMS is not just a procedural entity however; it’s core to effective business strategy. Integrating a QMS should align with and support broader organisational objectives, offering a structured framework for managing processes, resources and information.
Key benefits across all the clients I have worked with include reduced errors, heightened efficiency and enhanced customer satisfaction, all through improved quality.
Real-world benefits
Real-world examples from Singlepoint’s own customers underscore the transformative impact of a properly implemented QMS. Take NGF Europe Limited, a St. Helens-based glass cord manufacturer.
Their Quality Manager, Mark Horton, noted that before implementing Singlepoint, their existing QMS was fragmented and misaligned with business needs. Post-implementation, Singlepoint revolutionised their approach, aligning key processes with internal and customer requirements. This led to a significant reduction in non-conformances and bolstered their ‘Right First Time’ manufacturing approach.
Similarly, Acdopro, a global manufacturer of laundry products, leveraged Singlepoint to improve multiple aspects of their operations, including document control and issue resolution. Their Technical Manager, Jack Hough, highlights in our case study how the system’s intuitive design and custom modules like Scale Data Collection streamlined processes and improved efficiency. The electronic document control system replaced cumbersome physical signatures, speeding up approvals and ensuring compliance.
Jack also touched on the importance of team buy-in for the platform to establish it as a single source of truth:
“Each and every person in our organisation uses Singlepoint and they all know how important it is to use the information within the system and only that information.
Best Practices for Implementation
The successful implementation of a Quality Management System hinges on several key ingredients, each playing a crucial role in the system’s overall effectiveness. At the heart of these ingredients are senior level sponsorship, peer level ownership and workforce engagement.
Senior Level Sponsorship and Peer Level Ownership
The involvement and endorsement of senior management cannot be overstated in my experience. Their sponsorship signals the importance of the QMS throughout the organisation, driving its acceptance and integration into the corporate culture. Equally important is the ownership of these processes by peers at every level. When individuals at all levels take ownership of the QMS, it fosters a sense of responsibility and commitment, crucial for the system’s sustainability and effectiveness.
Project Champion
From my experience in numerous customer QMS implementations here at Singlepoint, I have always found a dedicated project champion, acting as a representative for the customer is vital to success. Their goal should be to facilitate internal communications, set priorities and ensure that internal needs are consistently met. Their role is instrumental in bridging the gap between the QMS vendor’s team and the customer, ensuring that the system aligns with user needs and business objectives.
Regular Review Meetings
This point goes hand in hand with appointing a project champion. While time-consuming, regular review meetings are essential for the success of the implementation project. These meetings allow for open communication, where both the QMS vendor and customer can report back on progress, address issues, and discuss changes. Such consistent engagement not only advances the project but also cultivates a strong working relationship between both sides, which is paramount for successful delivery and ongoing iterative improvements.
Measurable Processes
A fundamental tenet of quality management is the continuous improvement of processes. However, improvement is only possible when processes are measurable. Implementing processes that you can monitor and evaluate is vital. This may require investments in equipment, software, or training, enabling accurate and effective measurement. Without this capability, it’s challenging to identify areas for improvement, ultimately compromising the QMS’s effectiveness in both the short and long term.
The Power of Quality Training
Underestimating the impact of well-designed, quality training can be a significant oversight in implementing a QMS. Education is the bridge to understanding; when people at all organisational levels grasp their roles and the required actions, the QMS’s effectiveness is markedly enhanced. This understanding isn’t just about knowing what to do; it’s about comprehending why these actions are necessary and how they contribute to the overarching goals of quality management.
Simplicity and Clarity in Documentation
In the realm of documentation, simplicity and visual clarity are your allies. Overloading documents with text can lead to confusion and disengagement. You should aim to keep documents concise, supplemented with graphical elements like flowcharts and diagrams.
These visual aids not only make the information more accessible but also more engaging. Ideally, these process flows should be electronic and interactive, swiftly guiding users to the information they need.
Frankly this is why we developed Singlepoint’s Visual Navigator, to ensure user interfaces within Singlepoint are easy and reflect real working environments.
Being ‘Always Audit Ready’
A critical best practice to embed in your QMS strategy is the principle of being ‘always audit ready’.
This concept might seem daunting, as many organisations are far from this ideal at the outset. Nevertheless, it’s a vital mindset. Every decision and implementation within your QMS should be scrutinised through the lens of audit readiness.
If an idea or process does not contribute to this readiness, it warrants a reevaluation. Ensuring that your QMS is perpetually prepared for an audit not only ensures regulatory compliance but also embeds a culture of continuous quality and accountability.
What Does a QMS Implementation Require?
To establish an effective QMS, several base components are essential.
Quality Policies and Objectives
These are the guiding principles and goals that define an organisation’s commitment to quality. They should align with the broader business objectives and be clearly communicated across the organisation.
Quality Manual
This document outlines the scope of the QMS, including the processes and procedures required to ensure quality. It serves as a reference point for employees and stakeholders and can be made available on the QMS itself.
Data Management Systems
Reliable data management systems like Singlepoint Business Intelligence are vital for capturing, analysing, and reporting data. This data is used to make informed decisions and track the effectiveness of quality initiatives.
Recommendations for Manufacturing and Engineering Companies
In the manufacturing and engineering sectors, implementing a Quality Management System requires a specific approach to ensure precision and consistency in production processes, with stringent control measures and clear tolerance guidelines to maintain product quality standards.
Integrating the QMS with supply chain operations is essential, encompassing thorough supplier quality management and material traceability. Singlepoint’s Supplier Management Module helps you to keep track of, and action, the multitude of criteria relating to managing your entire supply base.
Compliance and safety are crucial. Many compliance professionals are ultimately trying to develop an Integrated Management System (IMS) that encompasses Quality, Health & Safety and Environmental aspects and is compliant with industry standards like ISO 9001, ISO 45001 and ISO 14001.
This approach ensures a holistic compliance strategy that addresses multiple critical aspects of business operation and sources of risk. You therefore need to ensure your QMS is compliant with industry standards like ISO 9001 and helps embed safety protocols into everyday operations.
Utilising technology to perform real time data collection and analysis also plays a significant role in measuring performance across quality, safety and environmental performance and identifying areas for improvement.
Implementation Steps
Software selection
When choosing QMS software, I typically recommend customers prioritise these factors:
- Ensure the software supports relevant industry standards and certifications.
- Look for a range of modules that suit your current needs
- Choose software that can scale up with your organisation’s growth and adapt to evolving requirements.
In terms of evaluating the range of options out there, I also recommend you:
- Arrange demonstrations to assess the software’s functionality, ease of implementation, and user interface.
- Evaluate how user-friendly the software is for users of all technical abilities. If you’re migrating from an existing system, it’s worthwhile understanding what users like and dislike about the current solution to help inform a set of criteria for selection.
- Consider third-party feedback or reviews from current users to gauge real-world performance and satisfaction. Review sites like Capterra and G2 are worth looking at.
Design and Build
After selecting your QMS, the initial phase of implementation involves designing processes that meet the needs of the organisation and its customers. This includes:
- Creating Process Maps: These maps provide visual representations of processes, helping to identify key steps and potential areas of improvement.
- Documentation: Developing comprehensive documentation for all processes is essential. This documentation serves as a guide for implementation and a benchmark for evaluating performance.
- Establishing Roles and Responsibilities: Clearly defining roles and responsibilities ensures that each team member understands their part in the QMS. This documentation is also useful when setting access permissions.
Deploy
The deployment stage is where your QMS is put into action and integrated into the daily operations of your organisation.
- Phased Implementation: Introducing the QMS in phases, module by module allows for manageable implementation and minimises disruption. At Singlepoint, we often find customers start on Singlepoint Core, our off-the-shelf solution, then move to Singlepoint Professional as they develop and require bespoke configurations.
- Training: Providing thorough training is crucial for ensuring that all employees understand and can effectively contribute to the QMS.
Control, Measure and Continuous Improvement
An iterative ongoing review of your QMS’ performance is essential for maintaining the integrity and efficacy of your system long term.
- Internal Audits: Regular audits assess compliance and identify areas for improvement.
- Performance Tracking: Tracking key performance indicators helps measure the impact of the QMS on quality and efficiency.
- Document Management: Effective management of documents ensures that the most current procedures are always in use and easily accessible. Luckily Singlepoint has full Document Control and Management functionality.
- Management Review Findings: Regular reviews by management provide insights into the QMS’s performance and areas needing attention.
- Formulating Improvement Plans: Based on these reviews, improvement plans should be developed and executed to enhance the system’s effectiveness continuously.