This in-depth guide will explore the importance of NPI, its core stages, challenges, and how QMS solutions like Singlepoint can facilitate a more efficient NPI process.
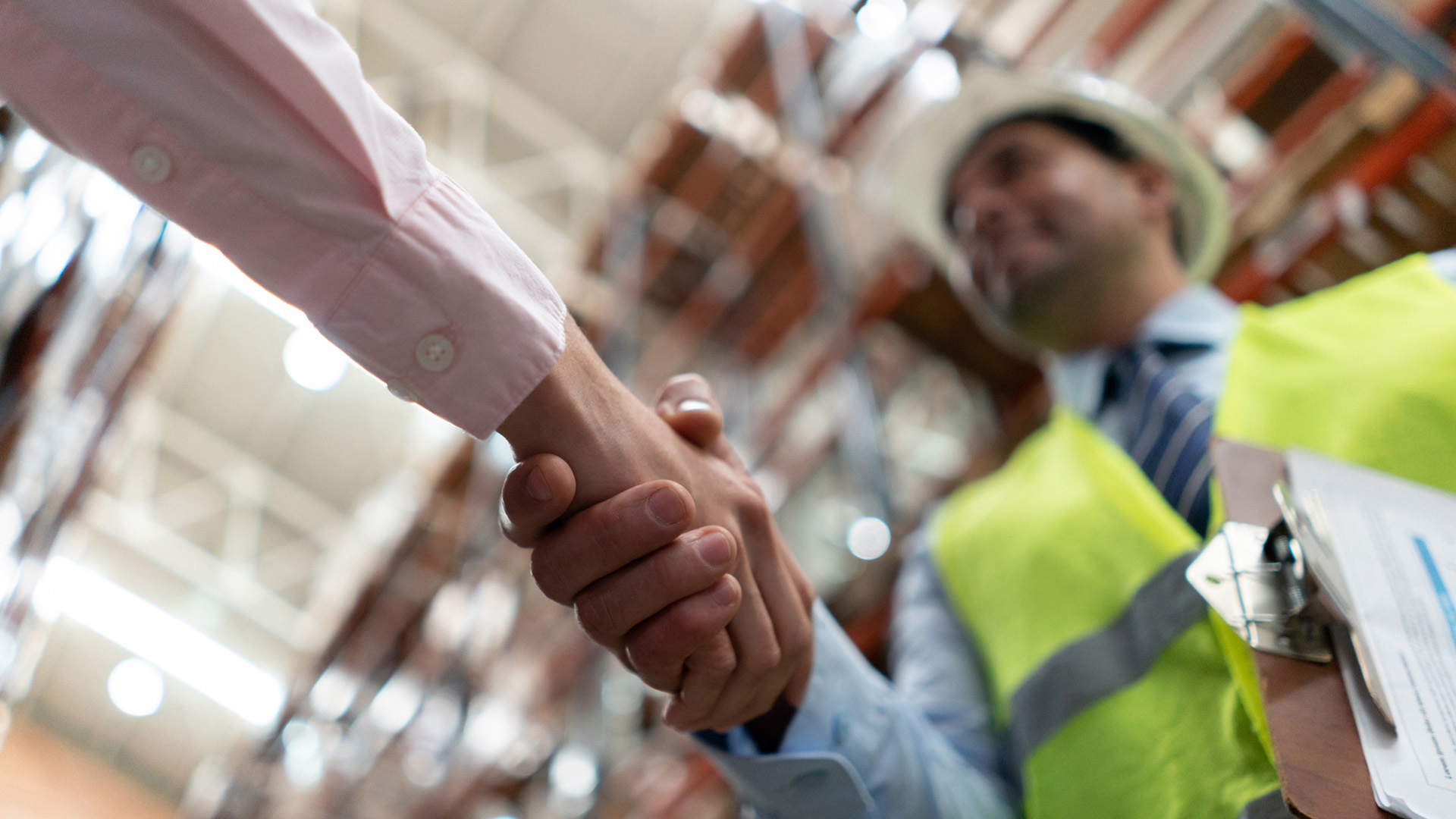
New Product Introduction Definition
Why is new product introduction important?
Goals of the New Product Introduction Process
- Developing innovative and competitive products that align with customer needs and preferences.
- Minimising risks, delays, and costs by effectively managing resources and time during product development.
- Ensuring seamless coordination and communication among different departments and stakeholders involved in the NPI process.
- Efficiently managing project timelines and budgets from inception to completion.
- Guaranteeing product quality, safety and regulatory compliance throughout the development process and beyond.
Why is it so difficult to launch a product?
- NPI requires input and collaboration from various teams, such as engineering, design, production and quality. Coordinating their efforts can be difficult, especially under tight deadlines.
- NPI processes can span months or even years, depending on the product’s complexity and market dynamics. Maintaining momentum, focus, and engagement during these extended time frames can be challenging.
- NPI projects involve numerous stages and tasks, each with its own deliverables and milestones. Managing this complexity requires careful planning, organisation and execution.
- Traditional project management tools, like Microsoft Project and Excel, may not provide the real-time data visibility needed for effective decision-making in complex NPI processes.
- Efficient communication is crucial for successful NPI, but reliance on conventional tools can result in communication gaps and inefficiencies that hinder progress.
How do Manufacturers implement NPI?
Alternatively, some teams use Excel to manage NPI projects. Although easier to use and more affordable than MSP, Excel lacks certain features and still leaves a considerable communication gap that needs to be bridged manually. Furthermore, both MSP and Excel fall short of offering a reliable method to attach supporting documents to individual tasks. Consequently, most project documentation ends up stored within Windows drives and folders, creating additional challenges in organisation and accessibility.
In addition to Microsoft Project and Excel, some manufacturers explore Product Lifecycle Management (PLM) software for managing their NPI projects. Larger enterprise systems in this category will cover more than just NPI, with their roots often embedded in 3D CAD systems.
Compared to Excel and MSP, PLM systems represent the extreme end of the spectrum. While they provide a comprehensive approach to managing product lifecycles, these systems come with their own set of challenges.
PLM software is typically costly and can be exceedingly difficult to implement, making it less accessible for smaller businesses or those with limited resources. Despite their robust capabilities, PLM systems may not always be the most suitable solution for every manufacturer’s NPI needs as the complexity and costs involved can outweigh the benefits.
As a result, many companies are turning to advanced software like Singlepoint to streamline their processes, enhance collaboration, and provide real-time visibility into project data from a single source of truth.
How APQP Supports NPI
This is guided by the overarching mantra – one version of the truth, compliance through control, visibility into real-time data and common collaborative workspace.
What are the key stages of new product introduction?
These tasks come with specified delivery dates and occasionally start dates, along with designated owners, which could be individuals, roles, or teams. Invariably, task completion necessitates the submission of supplementary data, often in the form of supporting documentation.
At any given time, each task holds a particular status, such as “In Progress,” “Complete,” or “Overdue.” These individual statuses come together to determine the status of the corresponding stage, which, in turn, contributes to the overall project status.
While an NPI project shares similarities with traditional projects, a key distinction lies in its repetitive nature. Unlike more free-form projects, which vary in composition, NPI projects often entail the same set of deliverables. However, it is important to note that variations in the NPI process can occur based on factors such as complexity, value, and risk. For instance, when introducing a groundbreaking product for a new or key existing customer, a more rigorous process might be necessary.
This is the typical outline of an NPI process:
Stage 1: Product Idea and Concept
In this phase, manufacturers and engineering firms will brainstorm innovative ideas and concepts for new products, taking into account market trends, customer needs, and technological advancements. This stage involves exploring various possibilities and identifying potential opportunities for product development. The voice of the customer is crucial in this stage, as understanding their needs and preferences is vital to exploring various possibilities and routes for product development.
Stage 2: Market Research
Companies will then assess the feasibility and profitability of the proposed product by conducting market research, technical evaluations and financial analyses. Incorporating the voice of the customer in this stage helps to again better understand the target audience and their expectations, as well as any potential gaps in the market the new product could inhabit.
Stage 3: Design and Development of Product
In this phase, companies will focus on developing and refining the product design. This involves incorporating customer feedback, findings from market research and industry best practices to create a product that meets clear specifications.
Stage 4: Pre-production and Prototyping
Firms will then plan the manufacturing process, considering resources, equipment and quality standards. They will also create prototypes for testing, evaluation and iteration, refining the design and manufacturing processes as necessary to ensure the product meets the required performance and quality benchmarks.
Stage 5: Manufacturing
Companies may need to invest in necessary equipment, tooling, machinery and plant resources, and validate their functionality through rigorous testing and inspection. If applicable, they may also need to identify, evaluate and select suitable suppliers for components and materials, considering factors such as quality, cost and lead times.
Stage 6: Product Launch
In this stage, companies will conduct testing and pilot production to ensure the product meets quality, performance and safety standards. Upon successful completion, they will initiate full-scale production and launch the product in the market.
Stage 7: Mass Production
As production continues, companies will closely monitor the production process to ensure ongoing quality and maintain efficient operations during mass production. They will also focus on optimising production capacity, reducing lead times and managing inventory levels to meet market demand and deliver products on time.
Stage 8: Innovation and Improvement Post-launch
Companies should continuously analyse product performance, customer feedback, and market trends to drive innovation and improvements in design, manufacturing and marketing efforts post-launch. This ongoing process ensures businesses can adapt to changing market conditions and enhance product offerings.
Who is involved in New Product Introduction?
- Product managers, responsible for overall project management and coordination.
- Engineers, responsible for product design, development and testing.
- Production teams, responsible for manufacturing the product.
- Quality managers, responsible for ensuring product quality and regulatory compliance.
- Suppliers, responsible for providing components and materials.
- Marketing teams, responsible for developing and executing on go to market strategies to successfully bring the new product to market.
- Regulatory and legal teams, responsible for ensuring compliance with all applicable laws, regulations and industry standards alongside the quality function.
- Procurement teams are responsible of the sourcing, purchasing and delivery of raw materials, components, skills and equipment required for the product development and manufacturing process.
Why Cross-Functional NPI is Important
How can software help manage the NPI process
Compliance-based process management: Compliance is seamlessly integrated into the process management system through customisable workflows, ensuring that the entire project team follows the defined process.
Real-time collaboration: Singlepoint provides a collaborative workspace where team members can communicate, share information and work together in real-time, fostering better decision-making and problem-solving.
Centralised document management: With Singlepoint, all project-related documents are stored in a centralised repository, making it easy for team members to access and collaborate on essential files, ensuring that everyone works with the most up-to-date information.
Supports multiple role needs: Singlepoint effectively caters to the diverse work styles of different team members. From providing project managers with top-down information or allowing individual users to concentrate on their specific tasks. By filtering out the noise, Singlepoint ensures that each team member can easily access and focus on the information they truly need.
Enhanced visibility and traceability: Singlepoint offers real-time visibility into project data, allowing stakeholders to track progress, identify bottlenecks and monitor key performance indicators (KPIs). This transparency helps keep projects on track and ensures that potential issues are addressed before they escalate.
Customisable workflows and project templates: Singlepoint allows users to create custom workflows and project templates tailored to their organisation’s specific needs and processes, ensuring a more efficient and streamlined NPI process.
Integration with existing systems: Singlepoint can be easily integrated with other enterprise software and systems, such as ERPs, and CRMs, ensuring seamless data exchange and reducing the need for manual data entry.
Advanced reporting and analytics: Singlepoint’s reporting and analytics features driven by Radar BI enable stakeholders to analyse project data, identify trends and patterns, and make data-driven decisions to optimise the NPI process.
Mastering the New Product Introduction process is critical for engineering and manufacturing organisations looking to stay competitive and achieve growth. By understanding the stages, challenges, and importance of NPI, as well as implementing comprehensive software solutions like Singlepoint, organisations can streamline their product development processes and significantly improve their chances of successful product launches.
Ready to transform your NPI process and experience the benefits of using Singlepoint?
Sign up for a free, no-obligation demo and discover how Singlepoint can help set every project up for success.