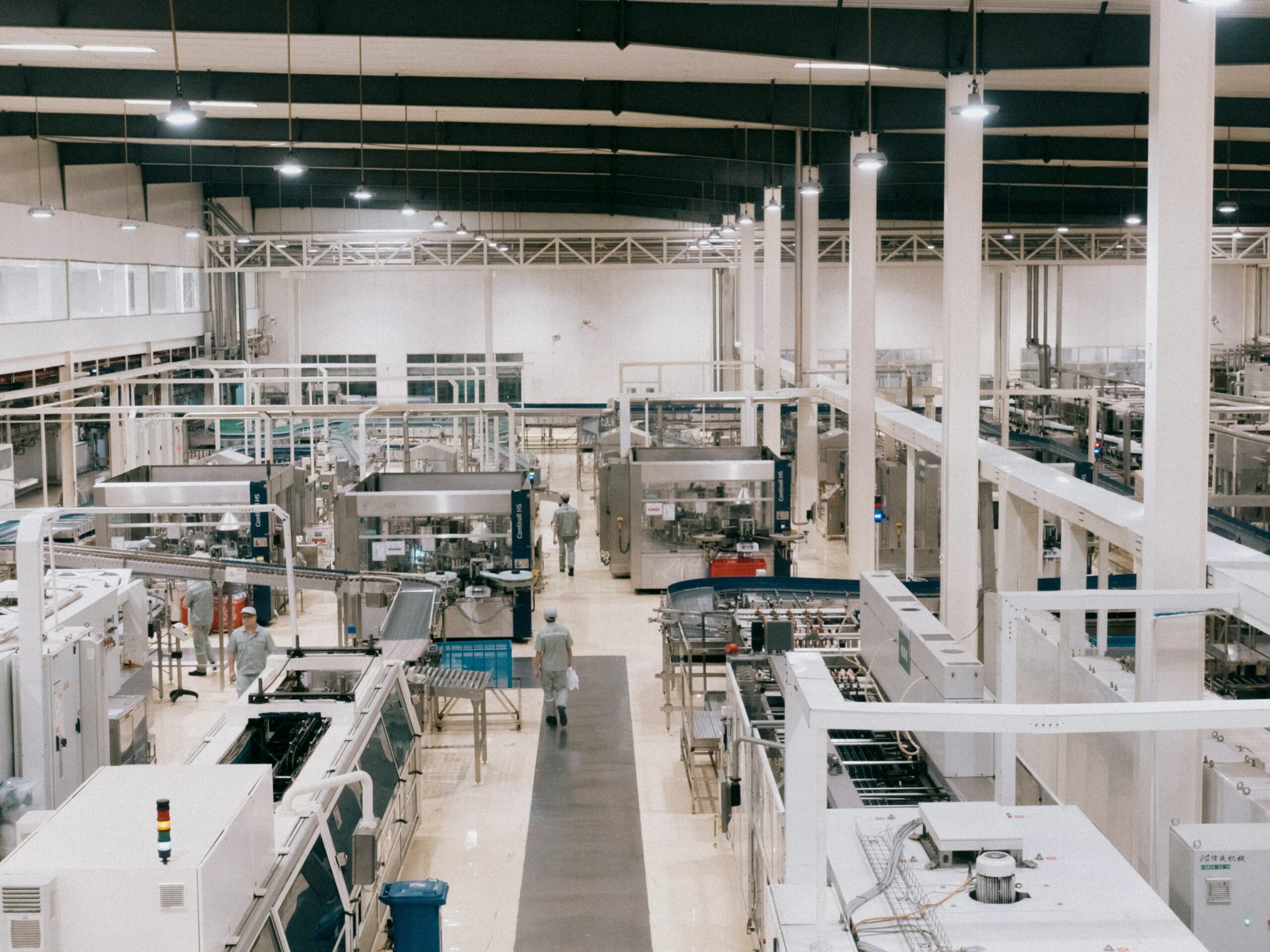
The Cost of Poor Quality (COPQ) quantifies the financial impact of delivering substandard products, encompassing costs from defects, failures and inefficiencies.
High COPQ translates to increased operational costs and reduced profit margins, making it a key focus for quality management. In some industries, the cost of poor quality can be as high as 20% of total revenue.
A robust Quality Management System (QMS) is essential in managing COPQ by systematically identifying and addressing these inefficiencies. Tracking COPQ provides valuable insights for optimising operations and setting priorities for quality initiatives, ultimately enhancing competitive positioning and enabling reinvestment in innovation.
Managing COPQ effectively is crucial for sustainable business practices and regulatory compliance. By minimising waste and improving resource utilisation, companies can reduce the risk of quality failures and associated liabilities. A proactive approach ensures quality issues are addressed before they escalate, supporting long-term business success.
Defining COPQ and COQ
COPQ is a subset of the broader Cost of Quality (COQ), encompassing all expenses related to ensuring and managing quality.
COQ includes not only the costs of poor quality but also the costs of good quality, such as prevention and appraisal efforts. Understanding the distinction between COPQ and COQ is crucial for identifying the right balance between investing in quality improvements and achieving cost savings by reducing defects and failures.
By focusing on both COPQ and COQ, businesses can make informed decisions on where to allocate resources for the most significant impact.
Components of COPQ
Internal failure costs
Internal Failure Costs are incurred when defects are identified before products reach the customer. These costs are directly linked to inefficiencies and errors within the production process that require internal correction, often causing operational disruptions.
In manufacturing, these costs often appear as waste and scrap from production errors, such as defective parts from a miscalibrated machine. In engineering, rework due to design flaws discovered late in the process can delay projects and increase costs.
Internal failures generally arise from process inefficiencies, including poorly defined procedures, insufficient training, and equipment malfunctions. These issues can be particularly problematic in complex industries, such as aerospace, where absolute precision is crucial.
External Failure Costs
External Failure Costs are incurred when defects are discovered after products have been delivered to customers. These costs can include warranty claims, product returns, and the expense of repairs and replacements. Additionally, logistical costs, such as travel and transit to deliver replacement parts or send personnel for repairs, can further increase these expenses, especially in industries like automotive and aerospace with complex supply chains.
Beyond the direct financial impact, external failures significantly affect customer satisfaction and brand reputation. Defective products can lead to decreased customer trust and loyalty, as well as potential loss of market share. The negative perception created by repeated failures can severely damage a brand’s image, making it challenging to retain customers and attract new ones. A notable example is the Samsung Galaxy Note 7 recall, which cost the company billions in direct and indirect costs due to the device’s overheating issue.
Appraisal Costs
Appraisal Costs are the expenses incurred from inspections and testing processes designed to ensure product quality before delivery to the customer. These costs are essential for verifying that products meet the required quality standards and for identifying defects during production, helping to prevent faulty products from reaching the market.
The role of inspections and testing is twofold: they serve as a safeguard to verify compliance with quality specifications and as a mechanism to catch and correct defects early in the production process. Effective appraisal activities can significantly reduce the likelihood of external failures, ultimately saving the company from more substantial costs down the line. However, these processes must be both thorough and efficient, as excessive or redundant inspections can inflate costs without corresponding benefits.
Prevention Costs
Prevention Costs are investments made to avoid defects and quality issues before they arise, focusing on proactive measures to ensure consistent product quality.
These costs include employee training programs to enhance skills and awareness, process optimisation to minimise errors, and comprehensive quality planning. Preventive maintenance and technology investments also play a crucial role, ensuring that instructional materials and best practices are easily accessible to those involved in production.
By prioritising prevention, companies can reduce the likelihood of defects and associated costs, leading to more efficient operations and higher-quality outcomes. This proactive approach not only minimises future failure costs but also contributes to overall operational excellence.
Calculating COPQ
Step-by-Step Guide on Calculating COPQ:
To accurately calculate COPQ, organisations need to gather data from various sources, including financial records, production logs, and quality reports. This data collection ensures all relevant costs are accounted for in each COPQ component.
The Role of Singlepoint in Data Collection:
Singlepoint plays a pivotal role in streamlining the COPQ calculation process through digitisation. The platform can help with:
- Embedding best practices: Integrates quality management into digitised workflows.
- Centralised data collection: This system acts as a “home” for all quality-related data, ensuring systematic and accurate tracking.
- Mandatory data provision: This ensures consistent data collection by making it mandatory on forms, with electronic approvals for accuracy.
- Accessible insights: Once data is embedded in the process, it becomes easily accessible through detailed reports and dashboards, enabling informed decision-making.
Collecting, Calculating and Analysing COPQ:
- Collect Relevant Data:
- Internal Failures: Costs related to defects, rework, and waste.
- External Failures: Costs from customer complaints, returns, and warranty claims.
- Appraisal Costs: Expenses from inspections and testing.
- Prevention Costs: Investments in training, maintenance, and preventive measures.
- Calculate Costs for Each Component:
- Use accounting data to determine the financial impact of each COPQ component.
- Apply formulas to quantify the cost of quality issues accurately.
- Analyse and Aggregate Costs:
- Sum the costs of all components to determine the total COPQ.
- Analyse trends and identify major contributors to COPQ.
- Review and Validate Calculations:
- Cross-verify data with financial and operational records to ensure accuracy.
- Validate the assumptions and methodologies used in the calculation process.
Impact of COPQ on Business
The financial impact of the Cost of Poor Quality goes beyond immediate expenses like rework, scrap, and warranty claims. One of the most significant yet often overlooked consequences is the damage to a company’s brand. Consistently delivering subpar products can lead to poor supplier scorecards, which in turn may cause the company to miss out on future requests for quotes and lucrative contracts. This loss of business opportunities can severely affect long-term revenue streams.
Additionally, addressing quality issues can drain resources that would otherwise be used more productively. Teams are often pulled into firefighting mode, attending meetings or travelling to customer sites to resolve issues. These activities not only incur direct costs but also lead to significant indirect costs, such as the opportunity cost of not being able to focus on other critical tasks. Over time, this reactive approach can reduce overall productivity and profitability.
Operationally, a high COPQ creates an imbalance where the focus shifts from preventing issues to constantly correcting them. This reactive stance can lead to inefficiencies and increased operational costs. In industries like automotive and aerospace, where precision is critical, the emphasis on “de-risking” processes through methodologies like Advanced Product Quality Planning and Six Sigma is vital. These approaches help embed best practices into production, reducing the occurrence of defects and improving quality over time.
Strategies to Reduce COPQ with your QMS
Overview of Software Tools and Methodologies Used in COPQ Calculation:
Reducing the COPQ requires a strategic and systematic approach, where leveraging the right tools and methodologies becomes essential. A robust QMS is at the heart of this effort, providing features and modules specifically designed to track defects, rework, and quality issues. Key components of a QMS include:
- Corrective and Preventive Actions for addressing and preventing recurring quality problems
- Issue Manager for tracking and resolving quality-related issues in real time
- Lessons Learned to capture insights from past experiences and apply them to future projects
A well-integrated QMS supports automated data collection and reporting, which is crucial for real-time monitoring of quality metrics. This capability allows businesses to gain accurate and timely insights, essential for effective decision-making.
With Business Intelligence tools embedded within the QMS, companies can benefit from detailed analytics and dashboards that highlight trends and pinpoint areas for quality improvements. Automated alert workflows ensure that stakeholders are immediately informed of emerging quality issues, enabling swift action to minimise operational impacts.
Integration with other enterprise systems like ERP and CRM enhances the effectiveness of a QMS. This integration allows for seamless data flow across departments, ensuring that all relevant information is available when needed. For instance, linking quality management with supply chain or customer relationship management systems provides a comprehensive view of how quality issues affect broader business operations and customer satisfaction.
In addition to a QMS’s technical capabilities, methodologies like Advanced Product Quality Planning (APQP) and Failure Mode and Effects Analysis (FMEA) are vital in reducing COPQ. APQP provides a structured approach to quality planning, ensuring potential issues are identified and addressed during product development.
FMEA systematically analyses potential failure modes and their impacts, enabling proactive measures before production begins.
Benefits of Using Quality Management Software for Accurate COPQ Assessment:
Implementing Quality Management Software offers significant benefits for accurately assessing and managing the Cost of Poor Quality. The key advantages include:
- Increased Accuracy and Efficiency
- Automated data collection reduces manual errors and effort
- Real-time tracking provides up-to-date information on quality costs, enabling more responsive management of issues as they arise
- Comprehensive Analysis and Reporting
- Integrated dashboards and reports allow for easy visualisation of COPQ data
- The ability to drill down into specific cost components helps identify areas for improvement, ensuring targeted and effective quality initiatives
- Improved Decision-Making
- Data-driven insights support strategic decisions that enhance quality and reduce costs
- The enhanced ability to prioritise initiatives based on their impact on COPQ ensures that resources are allocated where they will have the most significant effect
- Facilitated Continuous Improvement
- Ongoing monitoring and analysis help sustain quality improvements over time
- The QMS supports the implementation of corrective actions and preventive measures, ensuring that quality issues are addressed before they become more significant problems
These benefits are far more achievable once processes are digitised, following careful definition and design. By embedding these processes within a well-structured QMS, the data collected throughout the production cycle provides a meaningful payoff at the end, enabling more informed and effective management of quality and costs.